Построенные в 60-ые годы АЭС и склады для хранения радиоактивных отходов пора выводить из эксплуатации, пока они не стали настоящей угрозой. Какие технологии могут стать альтернативой ручному труду и почему в этой ситуации важно не только и не столько «железо», сколько умение им управлять? Об этом беседуем с Алексеем Кудрявцевым, генеральным директором компании «Брокк демонтаж Северо-Запад».
– Для начала подчеркну: «железо», то есть сами машины, конечно, важны. Роботизированные комплексы применяются во всем мире – их используют как для решения штатных задач на АЭС в Германии, Франции, Великобритании и в других странах, так и для устранения последствий аварий, например, на «Фукусиме», в Японии. Но там это рассматривается не в качестве альтернативы ручному труду, а как единственный возможный вариант: все-таки безопасность людей должна быть на первом месте, и только потом во внимание принимаются другие преимущества роботизированного демонтажа, а именно: широкий спектр применения при демонтаже, снижение дозовой нагрузки на персонал, сокращение сроков выполнения работ, отсутствие усталости у машин, сокращение влияния человеческого фактора и так далее. Особенно это актуально для зон на АЭС и хранилищ, где люди даже с серьезными средствами защиты могут находиться очень непродолжительное время. Таким образом, роботизированный демонтаж – это уже мировой стандарт.
– О каких именно роботах идет речь и на что они способны?
– Конкретно наша компания располагает парком шведских радиоуправляемых роботов – мы тесно сотрудничаем с представительством компании Brokk AB на территории России. Мы сделали ставку на мирового лидера в отрасли демонтажных роботов и ни разу не пожалели об этом. Компания, первой подарившая миру эту технологию, обладает высочайшим уровнем инженерно-технической поддержки, что важно во время выполнения сложнейших задач по демонтажу строительных объектов. Ведь сегодня демонтаж подразумевает широкий спектр задач: разборку и фрагментацию конструкций и сооружений, измельчение материалов, перемещение материалов, погрузку в транспортные средства, а в аварийных случаях и разборку завалов. Требуется перекусывать и резать металлические конструкции, делать проемы и проезды в армированных бетонных перекрытиях и стенах, укреплять неустойчивые перекрытия, где-то проводить частичный демонтаж внутри действующих помещений или же вовсе работать в условиях крайне высоких температур. На все это наши роботизированные комплексы способны.
Самая маленькая машина весит 500 кг и в ширину всего 597 мм, что позволяет ей совершать операции в крайне ограниченном пространстве, проходить в стандартные дверные проемы, перемещаться по лестничным маршам и в грузопассажирских лифтах, а если это необходимо, то и работать на непрочных, аварийных перекрытиях. Кстати, сравните: самая большая машина способна поднять груз весом до 3 тонн, тогда как рабочие имеют дело только с фрагментами до 50 кг максимум. Демонтажные роботы могут оснащаться видеокамерами, что позволяет оператору управлять машиной с безопасного места, а благодаря пульту дистанционного управления есть возможность подойти непосредственно к точке ведения работы, скорректировать действия, если требуется ювелирная точность. Большой плюс в разнообразии навесного оборудования – по факту получается, что одна машина Brokk заменяет собой несколько единиц узкоспециализированной техники, с возможностью смены навесного оборудования автоматически и дистанционно – оператору не придется входить опасную зону лично. В итоге дозовая нагрузка на персонал значительно сокращается даже при относительной чистоте рабочей зоны.
– Вы считаете, что одних роботов достаточно для решения таких задач?
– Разумеется, нет! Именно от согласованных действий наших инженеров и операторов роботизированных комплексов зависит безопасность, точность, грамотный выбор навесного оборудования, правильное позиционирование техники и в итоге – эффективность и производительность. Поэтому мы с гордостью можем заявлять о том, что наше ключевое преимущество – разнообразный опыт и стаж персонала более 10 лет. Мы начинали со сферы гражданского строительства. В конце 80-ых в метростроении наступили трудные времена, в результате в нулевые все еще использовался тяжелый ручной труд проходчиков. Совместно с метростроителями мы начали внедрять средние машины и доказывать заказчику, что каждая из них по производительности превосходит любую бригаду из 8 проходчиков, устававших к концу смены, в то время как машины работали бесперебойно. С нуля выращивали команду операторов, которые могут управлять этими машинами в тяжелых условиях ограниченного подземного пространства – например, в тоннелях всего до 1,5 метров в диаметре. Также у компании есть опыт устранения последствий аварии на Саяно-Шушенской ГЭС: 2 машины трудились в разрушенном машзале, где в любой момент могло произойти обрушение перекрытий. Как вы понимаете, при ручном демонтаже для персонала это могло обернуться самыми серьезными последствиями, а дистанционное управление и возможность смены навесного оборудования для разрушения бетона и резки металлов без присутствия человека оказались огромным преимуществом.
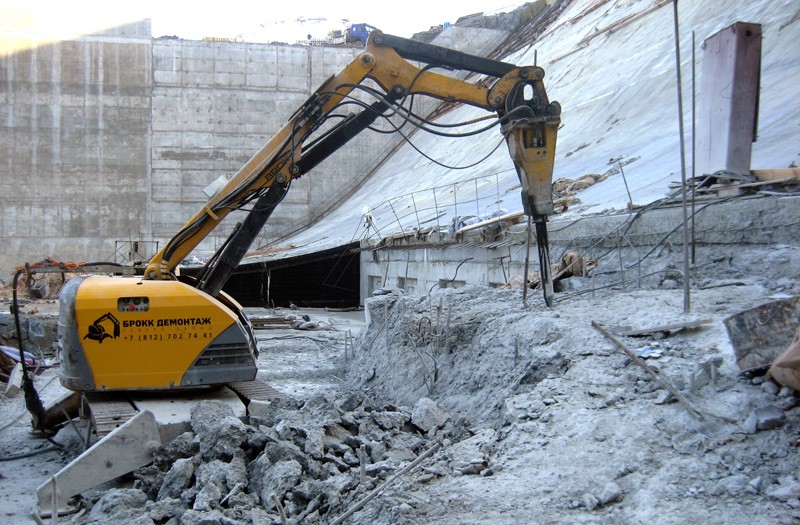
Вообще, у Brokk большой арсенал рабочих инструментов – гидромолот, ножницы по металлу, бетонолом, дисковая пила, фреза, захват и грейферный захват, ковш и грейферный ковш. Кстати, если комбинировать эти инструменты с дорогостоящей технологией алмазного пиления, можно снизить общие расходы до 80%! При этом уменьшаются вибрационные нагрузки и значительно сокращается объем воды для охлаждения дисков и каната – воды, которую, отмечу, еще нужно собирать, очищать и утилизировать. Так что и в этом случае получается экономия усилий, времени и средств. Работали мы и в Сочи – на строительстве подземных коллекторов к Олимпиаде, где важно было не парализовать движение в городе. Габариты выбранных машин удачно позволяли не перекрывать всю дорогу, а ограничиваться только одной полосой. Параллельно мы тестировали удаленное управление – всю логистику выстраивали из Санкт-Петербурга.
– Однако у работы на АЭС своя специфика?
– Безусловно, операторам нужно пройти обучение и все необходимые инструктажи, получить допуск к работам на станции, больше внимания уделяется детальному – я бы даже сказал скрупулезному – планированию, подготовке и контролю всех вспомогательных процессов, а затем и демонтажных. В этом году мы получили возможность проверить нашу квалификацию на Нововоронежской АЭС, блоки которой по очереди выводят из эксплуатации. Работы очень сложные, огромное количество металлоконструкций, предназначенных для демонтажа. Наша задача состояла во фрагментации транспортно-технологического оборудования в зоне контролируемого доступа блока №2. Мы использовали робота с тремя видами навесного оборудования – уникальной дисковой пилой, ножницами по металлу и по бетону. Роботу нужно было пропилить защитный контейнер, фрагментировать погрузо-разгрузочную машину и переместить фрагменты на площадку для временного складирования. Мы выполнили поставленную задачу, сделали для себя организационные и технические выводы, оценили, сколько времени требуется на согласования, на получения допуска и т. д. Результаты нашей работы были представлены на конференции в Севастополе, мы получили хорошие оценки проделанной работы и качественную обратную связь с приглашением участвовать в проектах различных управлений и подразделений Росатома.
– Как применяются роботизированные комплексы в атомной отрасли?
– Например, для извлечения, фрагментации и сортировки радиоактивных отходов при ликвидации хранилищ твердых и жидких радиоактивных отходов. Напомню, что среди навесного оборудования есть захваты различного типа, а для высокоточных операций может использоваться копирующий гидравлический манипулятор Kraft. Следующий шаг – дезактивация поверхностей путем снятия слоев, для этого пригодятся фрезерная и вакуумная установки. Затем роботы помогут при рекультивации территорий – загрязненный грунт удалят с помощью экскаваторных ковшей, оснащенных дозиметрическими и радиометрическими приборами измерения, что, кстати, позволяет точно определить класс отходов и составить полагающийся паспорт. Добавлю, что мы совместно с инженерами Brokk AB можем разработать любые технические решения, с использованием трехмерного моделирования.
- Какое будущее, по вашему мнению, у роботизированных машин в атомной энергетике?
- Основываясь на международном опыте и выполненных проектах, можно уверенно говорить о том, что использование роботизированных средств для обращения с РАО и выводе из эксплуатации принесет только положительный эффект для атомной отрасли РФ, увеличит безопасность проведения работ и повысит их эффективность.